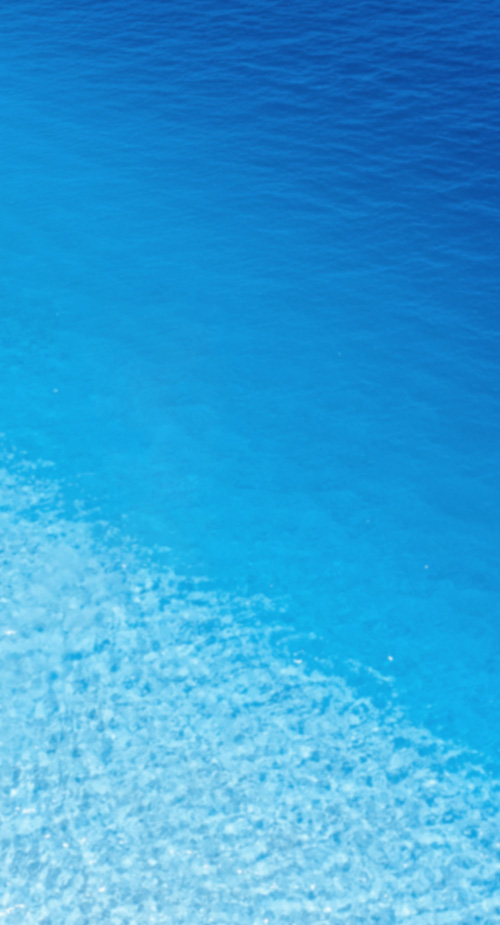
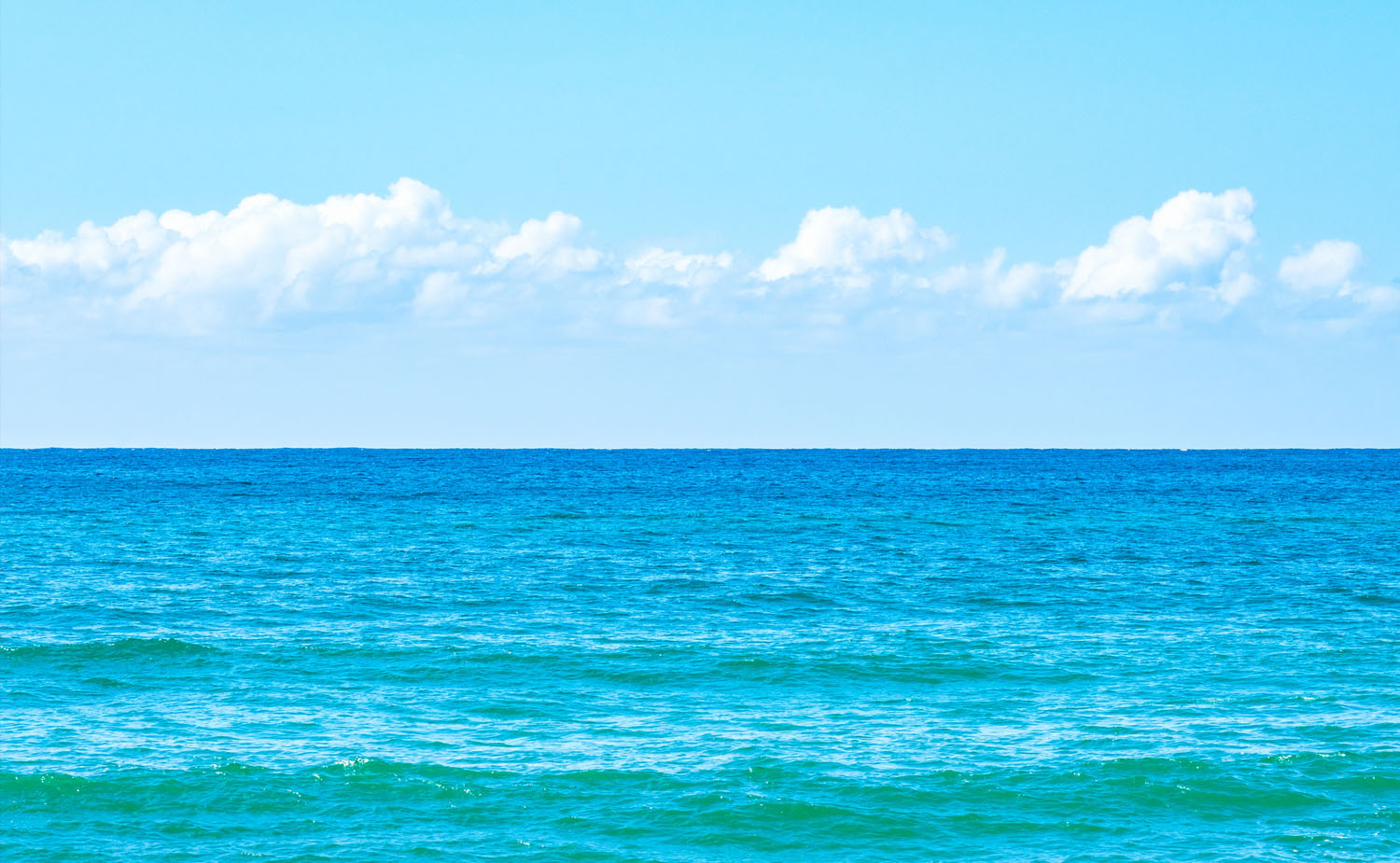
Stud Dowels
水中スタッド溶接
スタッド溶接は、いわゆる立込みボルトを穴あけ、タップ加工などの工程を経ずに、
アーク溶接により相手の母材に自動的に植え付ける方法であり、作業の性質上、この方法を「溶植法」と呼ぶこともあります。
Equipment Configuration
スタッド溶接装置
(水中および陸上)機器構成
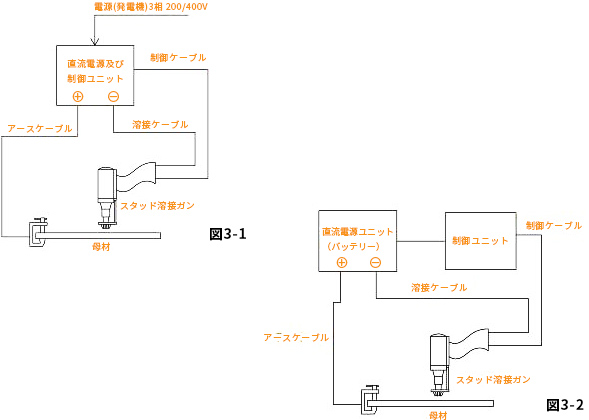
通常の陸上用機器の構成を図3-1に示す。
スタッド溶接装置は制御装置(現在は直流電源装置が内蔵されたものが主流)、溶接ガン、交流電源により構成されております。
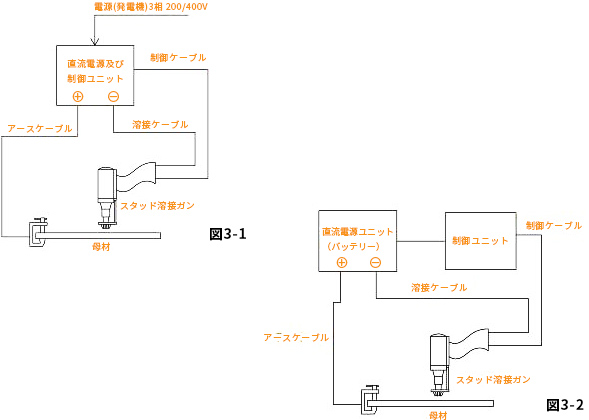
Characteristicスタッド溶接
(水中スタッド溶接)の特性
01 Weld strength 溶接部強度
スタッド溶接は、スタッド軸部全断面積が完全に融合される溶接方法なので、継手効率は100%であります。
したがってスタッド材料を試験用鋼板に溶接し、引張り試験等を実施した場合、溶接部ではなくスタッド軸部で破断します。
02 Stud material/Heat processing スタッド材質・熱加工
写真1 :通常の陸上用スタッド(熱処理無し)を使用し、水中スタッド溶接を実施したものですが、溶融金属部には急冷による溶接ワレが発生しております。この急冷による溶融金属内に発生する溶接ワレが水中スタッド溶接の機械的強度を著しく低下させる主要な原因です。
写真2:水中用スタッド(スタッドに特殊熱処理を施したもの。)を使用した溶接部のマクロ断面です。溶融金属部に異常も無く、機械的強度(曲げ、引張)に関しても問題ありません。
以上より、施工前にはテストピースによる試験等を実施し、設計強度を満たすスタッド材質の選定、スタッド熱加工処理方法の検討が必要です。
適切なスタッドの材質選定、熱加工処理等により、水中スタッド溶接におきましても陸上施工のスタッド溶接と同等の十分な強度は得られます。
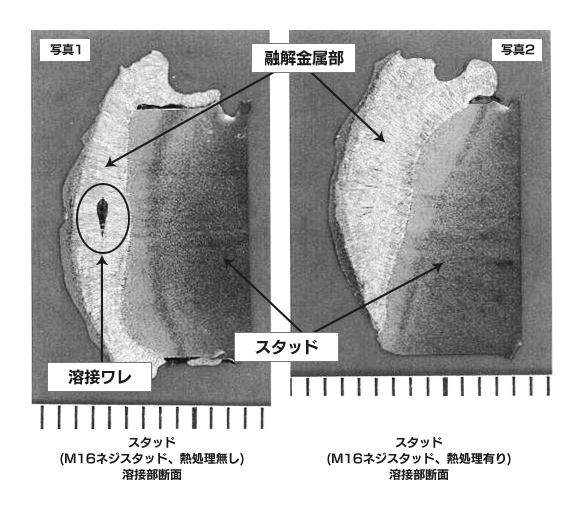
03 Appearance of Welded part 溶接部外観
スタッド溶接部にはフラッシュ(溶融金属が軸部外周にはみ出てアークシールド内で冷却、凝固したもの。)と呼ばれるものが形成されます。このフラッシュは他のアーク溶接時の隅肉と異なり、強度的な要素は持っていません。水中スタッド溶接の場合、陸上のスタッド溶接に比べ、溶接部が急速に冷却されるため、フラッシュの外観が悪くなることは避けられません。軸部溶接部分外のフラッシュの不整、フラッシュ外周ブローホール等は有害な欠陥とみなされません。
04 Base Material Thickness 母材厚さ
溶け落ちや極端なひずみを生じない為には、母材厚さはスタッド軸径に応じて下表に示す値より大きくなければいけません。
スタッド軸径 | 最小母材厚さ |
---|---|
13mm | 5mm |
16mm | 6mm |
Construction Management
水中スタッド溶接
施工管理について
水中スタッド溶接の施工管理は確立された規格等がないため、各工事ごとに発注者との協議により決定しております。
以下に陸上での橋梁等の検査を参考とし、水中において実施可能な範囲において、過去の実績を基に、材料、機器及び溶接条件が正しく守られているかどうかをチェックするため、弊社にて定めた管理項目例を示します。
01 Appearance of Welded part 溶接部外観
本検査は施工条件(溶接熱量設定)が適正であるかどうかをチェックするためのものです。
1. 試験片数量試験片の数量は、最低1工事単位ごとに、引張試験、曲げ試験各々3本ずつとします。
2. 試験片の製作試験片は図1の様に製作します。
※(A)試験材は引張及び曲げ試験用に分割するため、分割したものに溶接した物も可。
3. 試験方法及び判定基準
曲げ、引張試験試験方法は図2、図3に、判定基準は表1に示します。
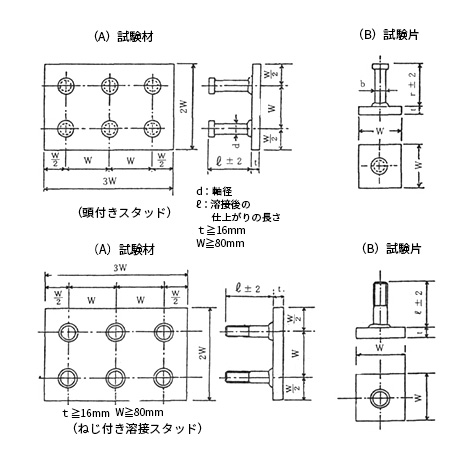
図1 試験材及び試験片の形状・寸法
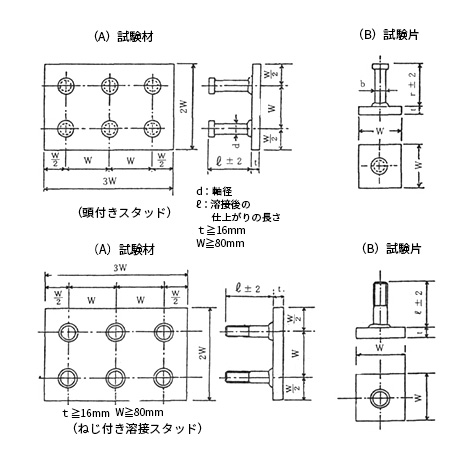
図1 試験材及び試験片の形状・寸法
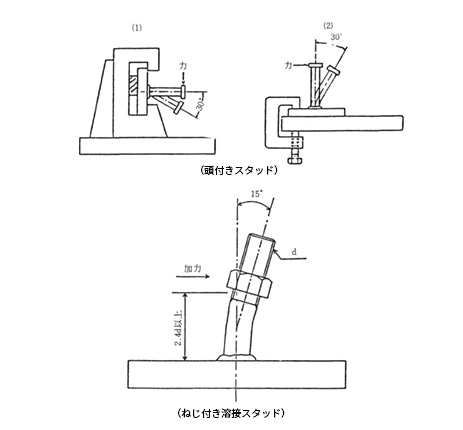
図2 引張試験状況
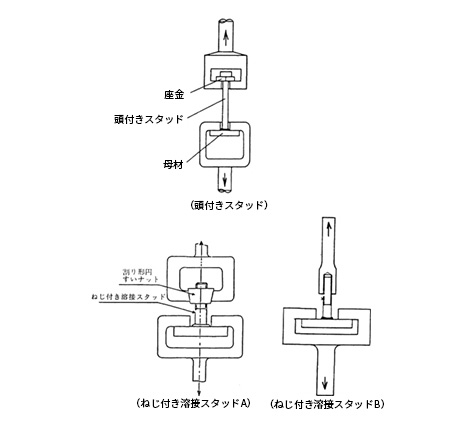
図3 曲げ試験状況
試験項目 | 試験片形状 | 試験本数 | 試験方法 | 判定基準 |
---|---|---|---|---|
スタッド 引張試験 |
図1による |
3 |
図2による |
溶接部以外で破断し、その引張強さが400~500N/mm2の時合格。 |
スタッド 曲げ試験 |
図1による |
3 |
図3による |
溶接部に割れを生じてはならない |
02 Pre-construction Management (inspection) 施工前管理(検査)
1. 承認されたスタッド溶接機器、スタッドボルト、フェルールなどの確認。
2. 溶接面の清掃(サンダ-ケレン)の良否を溶接前に(溶接技術を持った)潜水士により目視確認。
3. 施工前検査に合格した条件(熱量)又は溶接実験データによる最適熱量範囲が正確に守られている事の確認(陸上監視員による溶接機設定の確認)。
溶接状況のビジグラフによる確認(ビジグラフは溶接電流と溶接時間の関係を示したグラフ(図4参照)であり、陸上監視員のグラフの見方(管理方法)としては以下のとおりです。)。
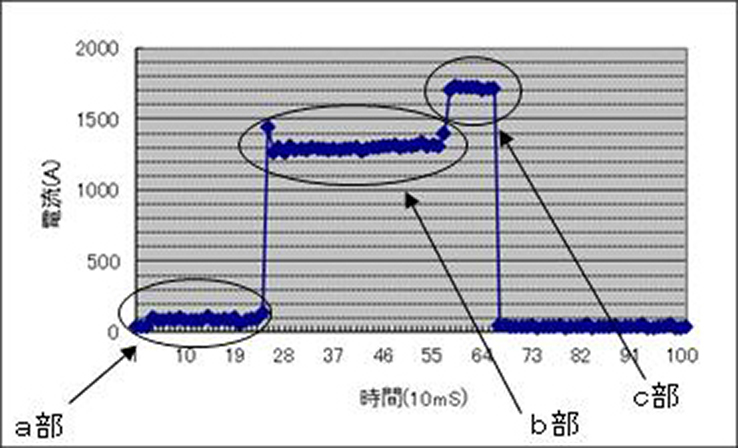
図4 ビジグラフデータ(電流・溶接時間管理記録)
■ 横軸に時間(単位10ms)、縦軸に電流(A)を取ってあり、(a)部はパイロッ トアーク、(b)部はアーク溶接時間、 (c)は短絡時間を示している。
■ 施工中に管理する部分としてはアーク溶接時間((b)部)は適切な範囲(電流と溶接時間の関係は別紙「「水中スタッド溶接」溶接時間について」参照、但し弊社の溶接機は一定時間(10ms)毎に電流値を測定し加算していくため、熱量は適正値に自動調整となります。)にあるか又、母材を貫通した場合、電流値が大きく触れるため、アーク電流波計の監視。
■ 短絡時間((c)部、溶接後、溶融地にボルトが入り込んだ状態、溶接完了)の電流増加が発生している事の確認。
母材を貫通したり、溶融金属が流れ出てきてしまった場合この短絡時間の電流増加が発生しません。
03 Post-construction Management 施工後管理
1.アークシールドからの溶融金属漏れ有無の潜水士による目視確認。
2.スタッド軸部に母材の異常(穴明き等)が生じていない事の目視確認。
Electrocution Safetyバッテリー式
スタッド溶接機の
感電に関する安全性
弊社所有のスタッド溶接機は電源をバッテリーとしています。電源をバッテリーにすることにより、水中スタッド溶接作業の感電における、交流電源に対する安全性を以下に示します。
一般的な水中スタッド溶接装置は陸上の溶接機をベースとし、溶接ガン等に防水加工等を施し、水中での使用を可能としています。そのため、現場作業の場合、機械の構成としては、交流発電機(150KVA以上)⇒直流溶接電源⇒制御装置⇒溶接ガンとなり、交流電流を直流溶接電源内の変成器、半導体素子等により整流し、直流として溶接に使用しております。そのため、交流成分は常に含まれ、半導体素子等の故障により交流成分の流出拡大の可能性があります。
弊社開発の溶接機の構成は電源ユニット(バッテリーユニット)⇒制御装置⇒溶接ガンとなり、電源はバッテリーのみを使用しているため、交流成分が入ることは一切ありません。
水中における実際の溶接作業時の感電について考えます。潜水士が水中スタッド溶接時に、構造物のアースを取った箇所(矢板、鋼管等)と溶接個所の導通が不十分(絶縁状態)で水中を電流が流れた場合、人体に流れる電流としては
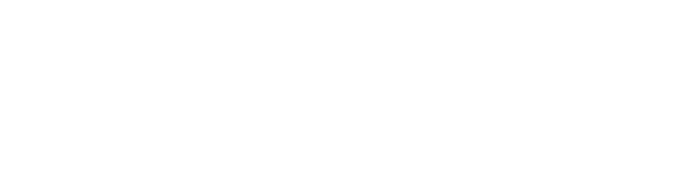
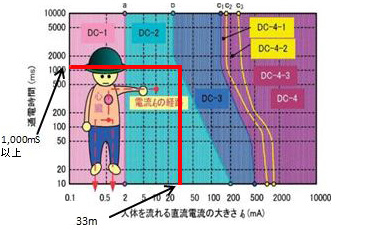
図1 直流電流に対する人体の反応(IEC60479-1を参考に作成)。
DC-1 | 通常無反応、わずかに刺すような痛み。 |
---|---|
DC-2 | 通常有害な生理的影響はない。 |
DC-3 | 心臓に回復可能な障害と伝達障害が起きる可能性がある。 |
DC-4 | 危険な病理生理学上の症状、例えば重度のやけど等が想定される(DC-4-1:心室細動の確率は約5%以下、DC-4-2:約50%以下、DC-4-3:約50%以上)。 |
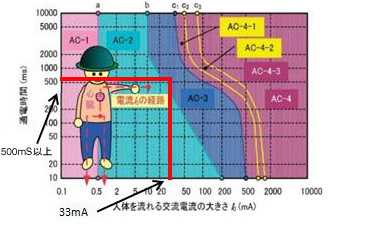
図2 交流電流(周波数:15Hz~100Hz)に対する人体の反応(IEC60479-1を参考に作成)。
AC-1 | 通常無反応。 |
---|---|
AC-2 | 通常有害な生理的影響はない。 |
AC-3 | 電流が2秒以上継続して流れるとけいれん性の筋収縮や呼吸困難の可能性がある。 |
AC-4 | 心停止、呼吸停止、または重度のやけどといった病理生理学上の危険な症状が引き起こされることがある(AC-4-1:心室細動の確率は約5%以下、AC-4-2:約50%以下、AC-4-3:約50%以上)。 |
CONTACT お問い合わせ
弊社へのお仕事のご依頼、
ご相談などはこちらから